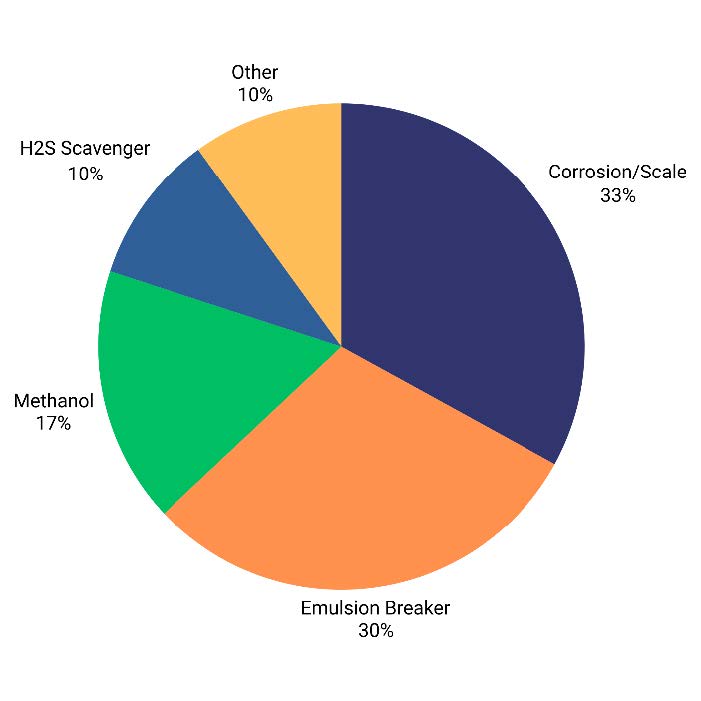
Background
In Spring/Summer of 2024, a strategic partnership was formed between Smart Chemical Services (SCS) and an actively horizontal well drilling produce in the STACK in Oklahoma. This collaboration stemmed from challenges with flowbacks, which were swiftly addressed thanks to the combined expertise of SCS’s Research and Development (R&D) and Account Teams. Their focus was on emulsion accelerating the oil and water separation processes. This allowed for precise fluid measurement and ensured that the oil met the contract parameters, ensuring smooth operations.
The successful resolution of the flowback issues earned SCS the trust of the operator’s key decision-makers. As a result, SCS was awarded two assets for comprehensive chemical treatment. The objective of this award was to optimize chemical performance while simultaneously reducing the overall chemical investment, demonstrating SCS's commitment to improving efficiency and value for their client.
Survey Findings
In the Spring of 2024, a comprehensive field survey was conducted, revealing several key findings. A primary concern was the elevated corrosion rates and high scaling potential across most of the horizontal wells, indicating a clear need for corrosion and scale inhibition products. Additionally, emulsions were observed in all horizontal batteries, leading to the decision to implement Emulsion Breakers (EBs) to enhance the separation process.
The survey also identified elevated levels of hydrogen sulfide (H2S) in the gas phase, which highlighted the necessity for scavengers to mitigate these issues. Another significant observation was that the chemical pump rates exceeded the target by over 40%, signaling a need for optimization of chemical application. These findings pointed to several areas where targeted chemical treatments could improve performance and reduce cost.
Smart Chemical Solutions Account Stewardship Excellence
In the effort to lower chemical investment while maintaining high performance, the selection of the right products became paramount. The primary focus was ensuring that the chosen products would deliver the necessary results to address the identified challenges. The following products were selected as part of the new program rollout:
- Corrosion/Scale Inhibitors – To address elevated corrosion rates and the high scaling potential across most horizontal wells, these products were chosen to protect infrastructure and optimize production.
- Emulsion Breakers (EBs) – These were selected to combat the emulsions present in the horizontal batteries, improving the separation process and facilitating more accurate fluid measurement.
- Paraffin Control – Given the potential for paraffin buildup, these products were included to help prevent blockages and ensure the free flow of fluids in the system.
- H2S Scavengers – With elevated H2S levels identified, scavengers were included in the program to mitigate the risks associated with hydrogen sulfide and protect equipment and personnel.
Stewardship Excellence Delivers Chemical Investment Reduction
The goal was to strike a balance between reducing overall chemical spending and ensuring that the products used were effective in addressing the various challenges identified during the survey. By carefully selecting these products, SCS aimed to optimize chemical treatment while still meeting operational and contractual requirements.
In 2024, Smart Chemical Services (SCS) focused on minimizing chemical costs by closely monitoring treatment target variance, a crucial element in driving down expenses. The account team achieved an impressive target variance of just 3%, ensuring that the chemical treatments were applied as efficiently as possible. This precision in chemical application played a key role in reducing the chemical rate by 43%.
By combining a tailored chemical program, expertise in product application and accurate chemical treatment rates, SCS was able to generate a significant reduction in overall chemical investment. The result was a 60% savings in chemical costs, demonstrating how effective strategy, product optimization, and meticulous attention to treatment targets can achieve both operational efficiency and cost reduction. This success not only lowered the chemical investment but also aligned with the goal of maintaining product performance while reducing expenditures.